Master planning is the most valuable feature.
MS Dynamics AX Consultant at a manufacturing company with 1,001-5,000 employees
Master planning is the most valuable feature.
What is most valuable?
How has it helped my organization?
Moving our production process from forecasting only to a master plan, including demand forecast and supply forecast wish, is great progress.
What needs improvement?
- Production planning
For how long have I used the solution?
I have been using it for one year and it works perfectly.
Buyer's Guide
Microsoft Dynamics AX
August 2025
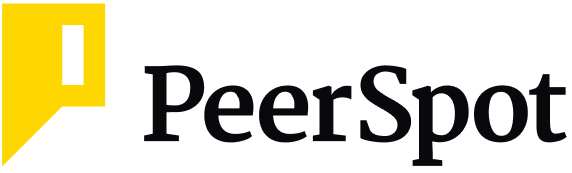
Learn what your peers think about Microsoft Dynamics AX. Get advice and tips from experienced pros sharing their opinions. Updated: August 2025.
865,295 professionals have used our research since 2012.
What was my experience with deployment of the solution?
In the beginning of our project phases, we faced a lot of issues related to collecting the master data but after that, every thing goes smoothly.
What do I think about the stability of the solution?
We have not encountered any stability issues related to the database; just some connection issues due to VPN connection stability.
What do I think about the scalability of the solution?
We have not encountered any scalability issues yet.
How are customer service and support?
Customer Service:
Customer service needed more improvement.
Technical Support:For all of the issues we faced, we found solutions in TechNet and handouts.
Which solution did I use previously and why did I switch?
We previously used MS Dynamics GP. Production and master planning is better in Dynamics AX.
Disclosure: My company does not have a business relationship with this vendor other than being a customer.
Dynamics AX / CRM Administrator at a tech services company with 51-200 employees
Generates financial reports that can be used with Excel. I would like to see improvements in manufacturing.
What is most valuable?
The finance and finance reporting features are good. The ability to use it with Excel means you can get the reports you need.
What needs improvement?
I would like to see improvements in manufacturing. We had a meeting with the person in charge of manufacturing last year in which I took six pages of notes regarding MRP/materials requirements planning. The implication was that the system can handle what we needed it do, but the person is charge of manufacturing is quite busy. I did not hear back after sending the notes, and I never helped implement it.
I do not think we have implemented it, and I think we still do it outside the system.
Some of the companies owned by the same parent company cannot implement this solution due to constraints on manufacturing.
It was a busy day when I toured the facility, and I had little time to discuss this solution. I just gathered that they could not make it fit for them.
For how long have I used the solution?
We have used this solution for a year.
What do I think about the scalability of the solution?
We encountered stability issues.
How was the initial setup?
The installation was complex. There are many settings to configure.
Which other solutions did I evaluate?
We previously used SAP.
What other advice do I have?
First evaluate if to see if it meets your manufacturing needs. In many settings, it does not.
Disclosure: My company does not have a business relationship with this vendor other than being a customer.
Buyer's Guide
Microsoft Dynamics AX
August 2025
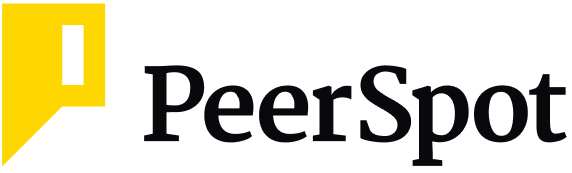
Learn what your peers think about Microsoft Dynamics AX. Get advice and tips from experienced pros sharing their opinions. Updated: August 2025.
865,295 professionals have used our research since 2012.
Microsoft Dynamics Consultant/Architect at a tech services company with 51-200 employees
With it, our inventory control is improved, but it needs cloud deployment and better documentation.
What is most valuable?
- Finance
- Inventory
- Manufacturing
How has it helped my organization?
- Improved inventory control
- GL consolidation
- Intercompany accounting
What needs improvement?
- Cloud deployment
- Documentation
For how long have I used the solution?
I've used it for seven years.
What was my experience with deployment of the solution?
There were some issues.
What do I think about the stability of the solution?
No issues encountered.
What do I think about the scalability of the solution?
No issues encountered.
How are customer service and technical support?
Customer Service:
It needs improvement.
Technical Support:It needs improvement.
Which solution did I use previously and why did I switch?
I was using Dynamics NAV, and we switched to AX due to limitations in Dynamics NAV.
How was the initial setup?
It's complex, in terms of data migration, but the latest version has improved a lot on this front.
What about the implementation team?
We did it in-house with involvement from a vendor team.
What's my experience with pricing, setup cost, and licensing?
The pricing model does not really fit all customers that I offer consulting too.
Which other solutions did I evaluate?
- SAP
- EPICOR
- Dynamics NAV
- Infor
What other advice do I have?
The product required extensive functional expertise for a successful implementation on all the areas, failed implementations of Dynamics AX has always lacked functional exposure
Disclosure: My company has a business relationship with this vendor other than being a customer. We're a consulting and implementation partner.
Business Analyst at StackEdge Consulting
It provides us timely access to management information, but it lacks reliable IT hardware and infrastructure both before and during implementation.
Valuable Features:
- ERP's major objective is to integrate all departments and functions across the organization and branches onto a single computer system that can serve all the department's particular needs.
- Timely access to management Information.
- Business Process Automation.
Room for Improvement:
- The non-delivery or non-availability of reliable IT hardware and infrastructure both before and during implementation.
- Pricing
- Proper training from skilled personnel
ROI:
Annual ROI = 7%
Disclosure: My company does not have a business relationship with this vendor other than being a customer.
Application Manager at a manufacturing company with 51-200 employees
Improving although still requires some attention
What is most valuable?
Flexibilty to allow change however this is its weakness as well. If you over develop core functionality it willing wrong.
How has it helped my organization?
Viewability of management data across all group companies. Introduction of consistent processes.
What needs improvement?
where different programmers have been let loose the product has a number of view inconsistencies and there are still issues that were in 4. Many bells and whistles have been added and some are not quite complete. Overall it is improving and becoming a more mature product.
For how long have I used the solution?
1 year on 2012. 8 years with 4
What was my experience with deployment of the solution?
Always down to number of development changes made to the core functionality. Data is also difficult to transform on day one.
What do I think about the stability of the solution?
As above, although testing minimises this risk
What do I think about the scalability of the solution?
so far, so good. Better scalability than 4.
How are customer service and technical support?
Customer Service:
Depends on the Partner as Microsoft tend to leave support to their Partners. This is the strategy they have which does mean that they may not get direct user feedback.
Technical Support:As above, can be a little hit and miss
Which solution did I use previously and why did I switch?
No
How was the initial setup?
The setup requires advance thought as it is difficult to amend once transactions are in the system.
What about the implementation team?
I have worked with a number of vendors and would say if you have the expertise in-house then use that.
What was our ROI?
Difficult to measure but definitely improved working practises and management information
Which other solutions did I evaluate?
SAP
What other advice do I have?
With care it is a good product but be aware that the business should change its processes rather than change the system wherever possible else you will have issues following deployment.
Disclosure: My company does not have a business relationship with this vendor other than being a customer.
VP Strategy & Solutions with 51-200 employees
Some resource capacity calculations could be expanded on, but it has reduced the time to payroll for expenses.
What is most valuable?
- Finance
- Projects
- Sales & Marketing
- Time & Expense
- HR
- Workflow
How has it helped my organization?
- Automated time-sheets
- Expenses with integrated mobile apps has reduced our time to payroll from three days to half day
What needs improvement?
Some resource capacity calculations could be expanded on.
For how long have I used the solution?
I've used it for two years.
What was my experience with deployment of the solution?
We didn't have any issues, and it was a very smooth transition for the end users.
What do I think about the stability of the solution?
We did an optimization post go-live for database indexes but otherwise fine.
What do I think about the scalability of the solution?
This is one of the strengths of Dynamics AX – scale up and out and it also deploys in the cloud.
How are customer service and technical support?
Customer Service:
It's excellent.
Technical Support:It's excellent.
Which solution did I use previously and why did I switch?
We just used very manual processes.
How was the initial setup?
Setup was easy and straightforward. We used Excel templates to load data and they had pre-configured versions of the application.
What about the implementation team?
It was an in-house implementation.
What was our ROI?
It took us 12 months to get an ROI.
What's my experience with pricing, setup cost, and licensing?
The original setup was approx. US$750k. The day-to-day costs are minimal.
Which other solutions did I evaluate?
We also looked at options from both Oracle and SAP.
What other advice do I have?
Make sure you understand your reporting requirements, and outcomes, prior to start of the project.
Disclosure: My company has a business relationship with this vendor other than being a customer. We are a Microsoft Gold Partner
Test Architect at a computer software company with 1,001-5,000 employees
Easy to use, reliable, and satisfactory technical support
Pros and Cons
- "One of the valuable features of the solution is how easy it is to use."
- "The integration could improve for the future."
What is our primary use case?
We are using the solution for a small organization.
What is most valuable?
One of the valuable features of the solution is how easy it is to use.
What needs improvement?
The integration could improve for the future.
For how long have I used the solution?
I have been using the solution for approximately 10 years.
What do I think about the stability of the solution?
In my experience, the solution has been stable.
What do I think about the scalability of the solution?
I have approximately 50 people using the solution in my organization.
How are customer service and technical support?
The technical support is satisfactory.
What about the implementation team?
We have a couple of technicians that do the deployment.
What other advice do I have?
I will continue to use the solution in the future and I recommend it to others.
I rate Microsoft Dynamics AX a nine out of ten.
Which deployment model are you using for this solution?
Public Cloud
Disclosure: My company does not have a business relationship with this vendor other than being a customer.
Director de servicios at KC ERP GROUP
Useful in retail, manufacturing, IT communications, and HR
Pros and Cons
- "The tool makes it easier to manage things."
- "Microsoft Dynamics AX needs to improve its support and the developer experience. Developing and programming are more complex. Automation and integration with other apps should be simplified."
What is our primary use case?
My clients' use cases for the product cover domains like retail, manufacturing, IT communications, and HR.
What is most valuable?
The tool makes it easier to manage things.
What needs improvement?
Microsoft Dynamics AX needs to improve its support and the developer experience. Developing and programming are more complex. Automation and integration with other apps should be simplified.
For how long have I used the solution?
I have been using the solution for more than ten years.
What do I think about the stability of the solution?
Microsoft Dynamics AX is very stable.
What do I think about the scalability of the solution?
The tool's capacity is big and can support hundreds of users.
How was the initial setup?
The solution's deployment is easy and similar to Windows.
What's my experience with pricing, setup cost, and licensing?
Microsoft Dynamics AX is not expensive.
What other advice do I have?
I rate the overall solution a nine out of ten.
Disclosure: My company has a business relationship with this vendor other than being a customer. Partner
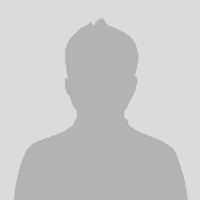
Buyer's Guide
Download our free Microsoft Dynamics AX Report and get advice and tips from experienced pros
sharing their opinions.
Updated: August 2025
Popular Comparisons
SAP S/4HANA
PeopleSoft
Oracle E-Business Suite
Microsoft Dynamics 365 Business Central
NetSuite ERP
IFS Cloud Platform
SAP Business One
JD Edwards EnterpriseOne
Epicor ERP
Microsoft Dynamics GP
BST Global ERP
Buyer's Guide
Download our free Microsoft Dynamics AX Report and get advice and tips from experienced pros
sharing their opinions.
Quick Links
Learn More: Questions:
- SAP ERP or Dynamics AX?
- Dynamics AX vs. JD Edwards EnterpriseOne
- Microsoft Dynamics AXL How satisfied are you with the solution?
- Comparing ERPs: SAP vs Oracle vs Microsoft
- When evaluating ERP, what aspect do you think is the most important to look for?
- Which is the best ERP for a mid-sized AEC company?
- Infor ERP SyteLine or SAP Business All-in-One?
- What would be your most recommended cloud-based ERP system for a medium-sized enterprise?
- Dynamics AX vs. JD Edwards EnterpriseOne
- Which ERP solution would you recommend for a construction company?
I had some clients go through the same issue - the AX manufacturing is generally good and we have some pharma mfgs doing process manufacturing and others doing discreet mfg - but AX is a LOT of work to configure and it takes a lot of consulting dollars.
So the issue is simply getting to the mfg implementation - I had one client that took 2 years before they brought everything up.
People are attracted to AX because it's so much less expensive than SAP or Oracle, but it's still a Tier One system - or very close to it.
So the best practice is to do the ROI study and come up with how it's going to make mfg less labor intensive - or whatever - and when the entire company sees the return, they will finally get behind the project and move forward.